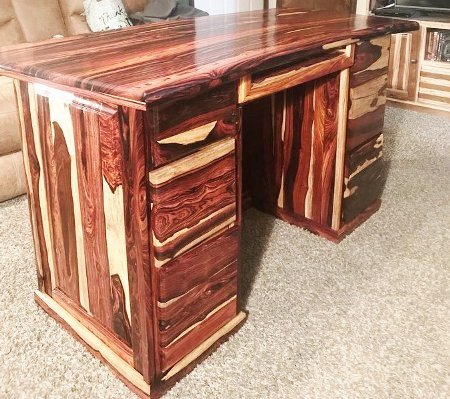
A cocobolo desk is made from a rare type of wood called cocobolo wood that's obtained from a tree (Dalbergia retusa) that grows up to 60 ft tall.
We believe you’ve probably landed on this page because you’ve always wanted to know how a cocobolo desk looks like.
Or you might have seen it on Better Call Saul.
In the spinoff series of Breaking Bad, there’s an episode called “Cobbler.” In the episode, Jimmy McGill orders a cocobolo desk as soon as he arrives at the law firm Davis & Main. The firm’s partner later tells Jimmy that only he has a desk that nice in the entire office.
Later on, Jimmy gets himself intentionally fired and writes the law firm a $7,000 check for the cocobolo desk. Omar then volunteers to drive a truck from Santa Fe to Albuquerque. On his return, he picks up the old desk and dumps it on the side of the road.
Cocobolo desks are very rare, as rare as the trees they are made from.
They are made from cocobolo hardwood, a type of wood that’s obtained from the slow-growing cocobolo tree. Since the tree takes many years to grow, it can’t be harvested quickly. This makes the wood’s availability low and its price high.
Cocobolo is without a doubt one of the most beautiful hardwoods in the world. Its alluring qualities have captivated artisans and woodworkers for generations.
A true rosewood, it belongs to the group Dalbergia. It is distinguished by the natural oil it produces which gives it a distinct, floral smell. It can also be polished to look glassy and lustrous.
Why is Cocobolo So Expensive?
Cocobolo desks are made from cocobolo, a tropical hardwood found in Central America belonging to the family Dalbergia.
Dalbergia Retusa, a medium-sized tree with a maximum height of 75-80 ft and a maximum diameter of 3 ft, is the species that contributes a lot of the wood used to make cocobolo desks and cocobolo furniture. However, there are two to three other species that also produce cocobolo wood.
It is important to note that only the heartwood of the tree is used. The timber is extremely valuable and the trees that produce it have been heavily harvested.
These days, it is rare to find the trees that produce cocobolo wood outside of plantations, reserves, and national parks.
Very small amounts of this precious wood get to the world market, which is why it is so expensive.
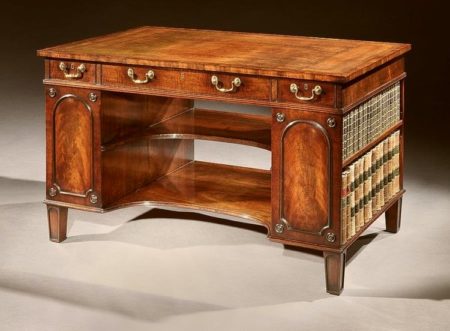
How Long Does a Cocobolo Tree Take to Grow?
These trees are slow growers and take a few decades to mature. The rare beauty and high value of this exotic wood, which has led to heavy exploitation of these natural forests, makes it difficult to find. The natural forests have been depleted and they currently grow on plantations across Central America. Harvesters must first acquire a government license.
Unfortunately, cocobolo desks are not sustainable for mass production. In the past couple of generations, the population of cocobolo trees has reduced by over 20%. This puts the species on the IUCN (International Union for Conservation of Nature) Red List as ‘vulnerable’.
How is the Wood Grain of Cocobolo Wood?
The wood grain of this lumber is straight to interlocked and showcases a myriad of colors including red, pink, yellow, purple, yellow, black, and blue. As the tree ages, its tone darkens. Experts advise the use of UV resistant varnishes to avoid darkening. It has an appealing and fine texture with a good luster.
The Cocobolo tree grows with several imperfections in its trunk, which makes it hard to get undamaged straight wood boards. This is another reason why a final product like a cocobolo desk is expensive. A single cocobolo desk can cost up to $15,000, although you can get it cheaper.
How Hard is Cocobolo Wood?
The Janka hardness test, named after the Australian-born immigrant Gabriel Janka, is the scale used to measure how soft or hard a piece of wood is.
Every piece of wood is given a number which is incredibly useful in determining how well it withstands dents, dings, and wear. The higher the number listed in the wood profile, the harder the wood.
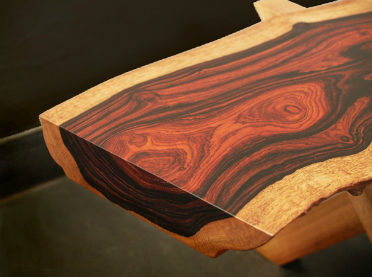
For example, basswood has a Janka hardness of 410 lbf (1,820 N), white oak has a Janka hardness rating of 1,350 lbf (5,990 N), while super-hard lignum is rated 4,390 lbf (19,510 N).
The latter is 3 times harder than white oak. Cocobolo wood has a Janka hardness of 2,960 lbf (14,140 N). It is almost twice as hard as white oak. In layman's terms, this wood is extremely tough, highly durable, and can withstand scratches and minor dents.
What Else Does Cocobolo Wood Make?
With the exception of desks, cocobolo wood is also used to make musical instruments like guitars, clarinets, flutes, bagpipes, oboes.
The wood is used to make fingerboards, entire necks, and bodies of guitars. It has been used as a substitute for Brazilian rosewood since the wood was added to the CITES Treaty in 1992 and its exportation was strictly banned.
Because it is very dense and hard, even a large block of cocobolo wood can produce a clear musical tone when struck. Cocobolo is also used to some extent when making some drums.
And because it is a very tough hardwood and can withstand exposure to water and repeated handling, it is commonly used to make knife handles, duck calls, and gun grips.
The wood is also used to make high-end cue sticks, brush packs, police batons, jewelry boxes, pipes, desktops, bowls, and many other expensive speciality items.
Cocobolo is used to make so many things because it is very hard, dense, fine textured, and easily machined.
The great thing about a cocobolo desk is that it is durable. Its oily nature makes it waterproof and resistant to scratching, insect attacks, rot, and age effects.
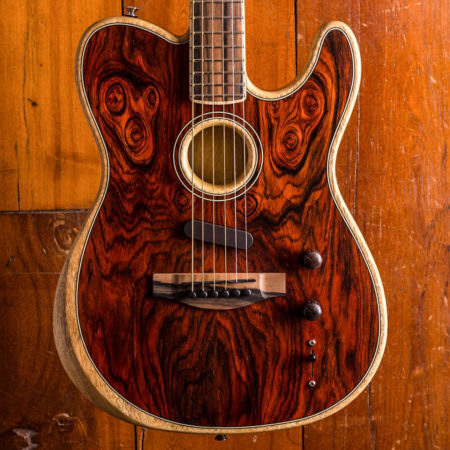
Is Cocobolo Wood Toxic?
No, cocobolo wood is not toxic. However, it is highly allergenic. The oil in the wood can cause allergic reactions if you inhale it or if it lands on your skin or eyes. We recommend that you wear full protective gear when working with this wood.
Cocobolo wood has also been reported to cause respiratory irritation and asthma-like symptoms. What causes the allergic reactions is the allergenic chemicals in the wood such as phenols and quinones. When machining cocobolo lumber, be sure to have a dust-collection method and protective equipment like respirators.
Where Does Cocobolo Wood Come From?
The origin of this wood is Central America, particularly Mexico, Guatemala, Nicaragua, Panama, and Costa Rica. Other names for this wood include Granadillo, Nicaraguan rosewood, Nambar, Palisander, Jacarandaholz, Pallisandro, Uruana, Caviuna, and Pau Preto.
Cocobolo trees grow very well in dry upland areas situated next to the Pacific coast. While the trees can reach a height of 80 ft, most only reach 60 feet and have diameters of 2 ft.
Some trees usually have 3-ft diameters, but these are extremely rare, not very tall, and poorly-formed. However, some wood experts believe that the most beautiful cocobolo wood comes from these trees.
Cocobolo wood is not only strong and durable, it is extremely beautiful, which is why it is renowned the world over. It has an irregular grain pattern and its color ranges from reddish-brown to dark red.
Cocobolo is used to make cabinetry, fine furniture, musical instruments, and inlays. It is not very hard to work with and is a favorite for carving and turning. It also finishes very smoothly.
The Three Main Species Of Cocobolo Wood
Mexican Cocobolo: This lumber features dancing and swirling patterns with dominant lines of black and dark purple and a background of red and orange. In a few cases, it’s the reverse.
Nicaraguan Cocobolo: This is a plantation grown lumber with a mix of black orange and red. They are not as appealing as Mexican cocobolo because they have fewer swirls.
Guatemalan Cocobolo: Although it’s almost identical to the Mexican kind, it’s less attractive due to its much lighter tones.
The Upsides of a Cocobolo Desk
Unique
A cocobolo desk is a vintage item. Its never on-trend, but never off either. With the timeless beauty and unmatched quality of this desk, you may not need to buy another desk for several years, unless of course, you choose to. It will emit a sharp spice-like odor for many years due to the fact that it is very oily and dense.
Easy to Work With
Cocobolo responds excellently to most hand and power tools in the process of turning, planing, and moulding. Also, nail and screw joints hold up well although predrilling is a wise decision. This wood sands very well to a waxy smooth finish even without applying finishing materials.
Can Be Mixed with Other Woods
If you’re having someone make the desk for you, instead of having a complete cocobolo desk, you can mix it with a different kind of wood for a unique contrast and aesthetic. For example, your desk could have drawers made from wood varieties like soft maple, cherry or walnut which are also beautiful.
The Downsides of a Cocobolo Desk
Expensive
Finding this type of desk at a decent price is not easy. This wood is in high demand but has a low supply, because the tree is found i tropical endagered rainforests.
Most desk manufacturers don’t use cocobolo wood to make their desks because it is expensive, hence they'll have to make the desks pricey.
However, if you can find one who has access to the wood and can expertly design a custom desk for you, then you’re in luck.
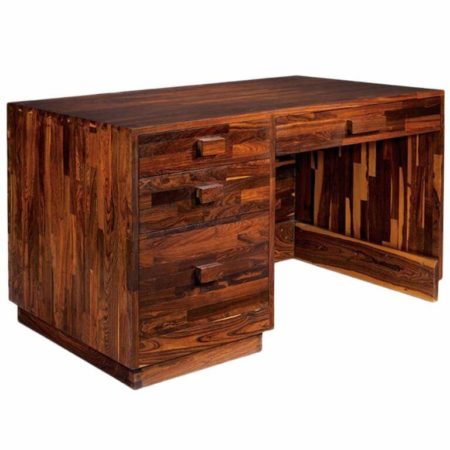
Dangerous to Make
The process of making a cocobolo desk is a somewhat dangerous endeavor. Like some other species, the cocobolo sawdust is toxic to humans and causes allergic reactions. Woodworkers that spend a considerable amount of time working around this lumber face all sorts of medical issues.
This lumber dust will cause eye irritations (pink eye), skin reactions, respiratory issues (asthma-like wheezing), and nausea. If inhaled into the lungs it may become lethal.
Anyone working with this wood should wear protective gear like masks, gloves and full bodysuits, uncomfortable but necessary. Also, thoroughly clean out your workshop area after working with this wood to avoid inhalation afterward.
Difficult to Glue
Besides the health issues it presents, this wood is difficult to work with, in the gluing phase of production. The wood is very oily and if you use a little glue, it will sink into the grain. To form a strong bond, the glue needs to penetrate the wood.
Woodworkers have attempted to sort out this problem by sanding the wood to open up the grain. Freshly sanded pieces tend to glue easily. Another solution is wiping the surface with a solvent like acetone and gluing immediately.
The high amount of natural oil in the wood makes it quite difficult to obtain a strong glue joint, especially when applying guitar fingerboards or veneers. The oil can also prevent the curing of some wood varnishes, especially oil-based ones.
If you don’t want to spend the whole day in the workshop trying to glue this wood, use acetone to remove surface oils before you start gluing. You can also remove surface oils using solvents such as lacquer thinner, denatured alcohol, naphtha, and mineral spirits.
Color Bleeding
Another challenge with this wood is that when you’re applying a finish, its color can easily bleed into any nearby wood. Interlocked grain can cause tear out while planning the wood. Also, the high density of this wood can cause a blunting effect on cutting tools, so they must be very sharp.
Dries with Difficulty
Craftsmen have mixed opinions when it comes to drying this wood. While some people believe that the wood dries excellently, other people disagree saying that it splits.
Some wood experts have advised craftsmen to season the wood in logs before cutting while other experts recommend air-drying after cutting, then kiln-drying. However, green wood taken straight to the kiln can get warped or checked.
In Conclusion
No doubt about it, a cocobolo desk is a beauty to behold. Its swirling and dancing patterns coupled with several color tones make it a coveted piece. Its other fantastic features are its high quality and durability.
The downsides of this rare piece though include the difficulties in the manufacturing process, its high price, and difficulty in finding it on the market.